Milling is a common machining operation that involves removing material from a stationary workpiece using a milling machine equipped with a spinning cutting tool. The workpiece remains stationary as the cutting tool spins and removes material as it presses against it.
Milling was improved significantly with the introduction of CNC. CNC programs are now capable of managing automatic tool changes, pallet changes, tool carousels, enclosures, and coolant systems. A machining center is a configuration that has these additional features.
Although all milling machines follow the same basic principle, each has its distinct qualities. This guide will compare horizontal milling machines and vertical milling machines.
What is a Vertical Milling Machine?

A vertical milling machine has a spindle that is vertically positioned and holds the collet that grips the cutting tool. This design is ubiquitous in CNC mills and is useful for milling, slotting, drilling, and boring.
Vertical milling machines are more popular in industries such as metalworking because they are less expensive than horizontal systems. The cutting head or spindle in these machines is vertically oriented. The specifics of milling controls can change between machines.
In the manufacturing industry, there are two types of vertical mills: turret mills and bed mills.
Turret milling machine
Turret milling machines are versatile because the spindle and worktable can move horizontally and vertically to the axis, allowing material manipulation in both directions. Because of their versatility in conducting different milling operations, they are a frequent investment in manufacturing plants. When dealing with larger pieces, however, there is a significant drawback because constructing them on a revolving bed becomes impossible. Due to the potential problems in generating two-axis motion for bigger components, turret milling machines are often better suited for smaller pieces.
Bed Milling Machines
Bed milling machines shift materials horizontally with a spindle confined to the vertical axis. The spindle moves up and down, shaping the material. These machines offer a broad range of movement, as the spindle’s vertical motion combines with the horizontal movement of the bed, enabling the milling of diverse shapes and depths.
Advantages and Disadvantages of CNC Vertical Milling Machines
CNC vertical machining centers have distinct advantages and disadvantages, making them suitable for various tasks. The benefits, primarily stemming from lower cost and greater availability, are counterbalanced by limitations in geometric design and cutting capabilities. The following pros and cons of a vertical milling setup will provide insights for informed decision-making based on specific job requirements.
Pros
- Easy to Operate: The structural design of VMCs provides operators with enhanced visibility, making it easier to identify and address potential issues during the milling process. The user-friendly CNC controls contribute to easy programming, reducing the time spent on setup and programming. This efficiency allows operators to focus more on ensuring that the project’s specifications are met, meeting the highest expectations in the process.
- Simplicity: Vertical milling machines are generally less complex than horizontal ones, making them more affordable and easier to use and maintain.
- Availability: The prevalence of vertical milling machines makes it easier to find the necessary parts or repair assistance when needed. This availability proves especially beneficial for those seeking a milling machine promptly, as vertical machines are generally more readily accessible. The commonality of vertical milling machines contributes to their ease of acquisition and potential for swift utilization.
- Versatility: Vertical machining centers come in different types. Turret mills are suitable for smaller projects, while bed mills handle heavier, larger workpieces, albeit less efficiently than horizontal mills.
- Footprint: Vertical milling machines have a smaller footprint than their horizontal counterparts. This, combined with their affordability, makes them attractive for smaller shops. The higher user base also means a larger pool of skilled machinists.
- Space: Vertical milling machines, in comparison to horizontal milling machines, occupy less floor space. For the owner of a small shop, this translates to having more available workspace or the ability to place additional machinery. The compact footprint of vertical milling machines can be advantageous in optimizing the layout and efficiency of a smaller workshop.
- Cost: Vertical milling centers are more prevalent and less expensive than horizontal ones, both in terms of initial machine cost and ongoing maintenance expenses.
- Detail: Vertical milling machines excel at milling fine features on parts with tight tolerances.
Cons
- Production Limitations: Vertical machining centers (VMCs) may struggle with higher volumes and complexities in production.
- Weighty Materials: Operations with heavier materials can pose challenges for vertical milling machines, as raising and lowering such materials can be more difficult.
- Access Limitations: While excelling at single-face milling (e.g., sinking dies), vertical milling machines are less adept at milling on all sides of a part, necessitating a new work-holding setup.
- Power Challenges: Handling very large and heavy parts can be challenging for vertical milling machines, especially turret mills that require constant movement of the workpiece.
- Speed: While accurate, vertical mills may be slower than horizontal milling machines in high-volume production scenarios.
What is a Horizontal Milling Machine?

A horizontal milling machine, like a vertical mill, may perform identical duties but is built differently, having a horizontally positioned spindle. These machines are stronger and more durable than vertical mills, allowing them to handle powerful cutting operations and large parts.
Horizontal mill cutters resemble circular saw blades, although they are often thicker, narrower, and engineered for faster milling than their vertical counterparts. The use of an arbor and its length enables horizontal mills to operate numerous cutters at the same time.
Some horizontal milling machines include a rotary table, which allows the cutting tool to approach the workpiece from varied angles for more intricate milling tasks. This is referred to as a universal table.
Advantages and Disadvantages of CNC Horizontal Milling Machine
Horizontal milling machines, like vertical setups, are a popular choice for a variety of applications, owing to their tool’s cutting power and ability to handle large-scale operations with high production demands. The system’s shortcomings, on the other hand, are primarily due to the increased expenses associated with obtaining and maintaining this equipment. Here is a quick rundown of the advantages and disadvantages of a horizontal milling arrangement.
Pros
- Improved chip evacuation: Metal chips produced during cutting can melt on the surface, causing flaws that may need post-processing. Horizontal cutters throw chips away, contributing to a superior finish on the material.
- Part complexity: Horizontal mills are the preferred option for intricate projects, offering greater versatility than vertical machines by working on more sides. They excel with heavier items and are ideal for cutting one or more grooves in a material. Horizontal milling machines are well-suited for creating slots and handling heavier materials. Moreover, these machines can accommodate additional cutters for various applications, enhancing efficiency in groove insertion. Some horizontal milling machines even allow the bed to rotate, enabling milling at multiple angles instead of solely on the horizontal plane.
- Enhanced stability: Horizontal machines feature thicker and shorter cutting tools, reducing vibrations and providing greater stability, especially during deep cutting operations.
- Capability for complex shapes: Horizontal mills offer the flexibility to handle different angles and incorporate add-ons, enabling the production of intricate shapes that may be challenging for a vertical milling setup.
- Speed: For high output and quick turnaround, a horizontal milling machine offers a faster cutting speed compared to a vertical milling machine. It can cut more than one piece at a time without compromising accuracy. This makes horizontal milling machines powerful tools for detailed or extended projects, where efficiency and precision are crucial.
- Increased Productivity: With a higher material removal rate, improved chip evacuation, and the ability to make deeper cuts in one go, horizontal milling machines facilitate more efficient operations, leading to higher productivity.
- Robust structure: The robust construction of a horizontal milling machine makes it heavier and capable of handling larger production batches. Each machine part’s structure, under specific working pressure, contributes to extending the overall service life. This sturdy design, compared to vertical mills, results in less vibration, reduced deflection, and a more stable operation, enhancing overall machine performance and durability.
Cons
- Costly: Horizontal milling setups are notably more expensive than vertical machines, involving substantial initial capital and maintenance expenses. Consequently, they are primarily found in large-scale manufacturing setups. For small businesses, opting for CNC machining services is a more viable alternative, eliminating the need for a significant financial commitment.
- Difficulty in finding expert operators: In addition to the elevated costs, locating skilled operators familiar with horizontal milling machines can be challenging. The scarcity of these machines means fewer individuals have hands-on experience, contributing to the shortage of trained operators.
Differences between Horizontal Mill vs. Vertical Mill

While there are numerous similarities between the two types of milling equipment, there are also significant differences. Now, let’s explore the distinctions in some key characteristics between them.
Differences | Horizontal Mill | Vertical Mill |
Orientation | In horizontal milling machines, the spindle, carrying the cutting tool, is positioned horizontally. The rotary cutter cuts into the surface and removes material from the workpiece while revolving around this horizontal axis. | In a vertical mill, the tool is set in a vertical orientation. These machines, resembling bench drilling setups, have a vertical arbor that holds and rotates the cutting tool, allowing it to plunge into the workpiece material as required. |
Tool Geometry | Horizontal milling machines use short and thick tools, ideal for removing substantial material from the workpiece. | Vertical milling machines employ long and thin tools. This variance in cutting tool geometry influences the nature and precision of the cuts each machine can achieve. |
Cut Specifications | The thick tools in horizontal milling enable it to swiftly execute deep and heavy cuts. Apart from standard cuts like facing and chamfering, horizontal mills excel in grooving and slotting operations. | Vertical milling machines handle general tasks well, with a focus on plunge cuts and drilling. They boast higher accuracy compared to horizontal milling machines. |
Cost | Horizontal milling machines have a higher initial cost, they compensate for it with improved time and production efficiency in the long term. Typically, well-established manufacturing companies with a history in the business invest in horizontal milling machines. | Vertical milling machines come with a lower price tag compared to horizontal ones. This affordability makes them increasingly popular in machine shops. The operational and maintenance costs are also lower, leading to overall savings in machining costs for customers.With a higher prevalence of vertical machining centers in the industry, there is a larger pool of skilled operators for these machines. |
Choosing Between Vertical Milling Vs Horizontal Milling Machines

Choosing between vertical milling and horizontal milling machines depends on several factors:
- Part Size: Consider the size of the parts you’ll be working on.
- Part Complexity: Evaluate the complexity of the parts you need to machine.
- Budget: Assess your budget for both machine acquisition and maintenance.
- Quantity: Determine the quantity of parts you’ll be producing.
- Machine Shop Availability: Consider the availability of the specific machine type in your machine shop.
- Material: Take into account the type of material you’ll be working with.
As a general guideline:
- Vertical milling is often preferable for detailed parts, single-sided work, softer materials, and projects with a limited budget.
- Horizontal milling is more suitable for rapid material removal, large and heavy parts, harder materials, parts requiring work on multiple faces, and operations that demand custom or specialist cutting tools.
In many cases, a machine shop will assess your project and recommend the best milling equipment based on these factors.
Factors Influencing the Choice of Machining between Horizontal and Vertical Milling
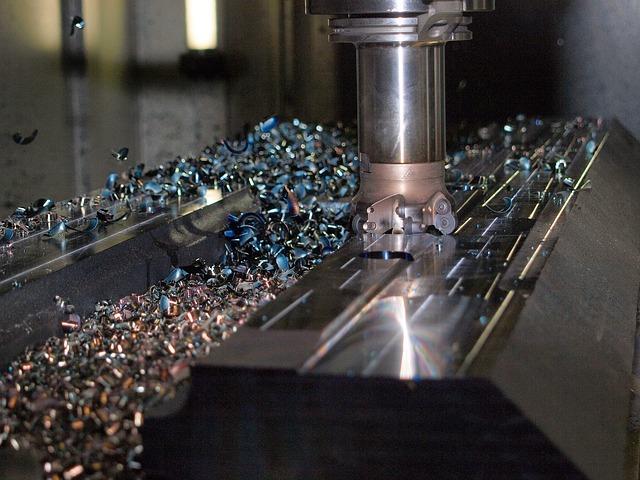
Although both vertical and horizontal machining centers can handle many similar cuts, each type has specific cuts that it excels at.
Other factors influencing the choice between the two machines include:
- Material Removal Rate
In terms of removal rate, horizontal milling machines outperform vertical ones due to their enhanced stability and capacity for deeper cuts. Vertical machines are commonly favored for specific tasks like facing and grooving, where the cuts are not as deep, allowing for precision. However, this limited cutting capability naturally results in a lower removal rate.
- Extent of customization
Each milling machine type can work with a range of tools, but the horizontal milling machine offers greater customizability compared to the vertical counterpart. Specific add-ons and cutting heads allow a horizontal mill to function as a vertical mill.
This versatility is particularly beneficial for manufacturing companies with only a horizontal machining center, enabling them to handle tasks typically done on vertical mills.
- Number of planes for machining
Vertical milling machines are preferable for machining on a single plane, while horizontal milling machines are the better choice when dealing with multiple sides that require machining at varying angles.
- The accuracy of the cut
Vertical machining centers are the preferred choice when high accuracy is a priority. Their design allows for precision in various machining operations.
- Operational Budget
The overall budget is a crucial factor to consider. If you’re setting up the entire milling machine setup in your workshop, it’s essential to note that horizontal milling machines come with a higher upfront cost and maintenance expenses. However, if you opt for a CNC machining service, the installation and maintenance costs of these machines become less significant.
Conclusion
Milling machines have advanced significantly in the last two decades, providing convenience in the creation of machine parts as well as different industrial advantages.
The synergy between modern vertical and horizontal milling is substantial, and understanding the distinctions is critical for making an informed choice. The information presented in this post should enable you to make an informed decision. Alternatively, you can choose CNC milling services from Zintilion’s CNC machining services, where our skilled personnel will determine the most cost-effective techniques for your project.
FAQ
What are the types of milling machines?
While there are various types of milling machines, such as column milling machines, C-Frame milling machines, bed-type milling machines, and more, the primary categorization often boils down to the orientation of the tool. This distinction leads to two main categories: vertical milling machines and horizontal milling machines. Understanding this fundamental classification helps in choosing the right type of milling machine for specific machining needs.
What are the main components of Horizontal Milling Machines?
Here is a breakdown of the key components:
- Column: Provides structural support for the entire machine and houses the oil reservoir and pump responsible for lubricating the spindle.
- Knee: Serves as the housing unit for the gearing mechanism inside the milling machine.
- Universal Table: This table secures the workpiece and allows machining from different angles.
- Spindle: Holds and supports the cutting tool of the milling machine.
- Overhanging Arm: A horizontal beam on the top face of the column, creating sufficient space between the structure and the tool.
What is the main difference between a vertical milling machine and a horizontal milling machine?
In vertical milling machines, the tool rotates on a perpendicular axis to the workpiece, resembling a cylindrical shape. On the other hand, in horizontal milling machines, the tool rotates around an axis parallel to the surface of the workpiece. This variance in tool orientation significantly influences the types of cuts and operations each machine is best suited for.
What are the limitations of CNC milling machines?
CNC milling machines come with a set of limitations, including size constraints, limitations on axis movement and degree of freedom, and tool capabilities. Additionally, the overall cost of CNC milling machines represents a significant limitation for many, impacting accessibility and affordability. It’s crucial to consider these factors when determining the suitability of CNC milling for specific applications.