One of the surface finishes used in machining is black oxide finish. Surface finishes are important in precision machining because they can extend the life and appearance of machined parts. One issue many finishes have is that they tend to increase the dimensions of the finished precise machine parts. Given the need for accurate measurements to fit in properly, this is detrimental to the functionality of these parts.
Black oxide finish, also known as blackening or gun bluing, is a conversion coating for ferrous materials (usually steel) that provides a layer which is corrosion resistant and enhances the aesthetic appearance of the metal.
However, the black oxide finish stands out compared to other metal surface finishes. This is due to its ability to impart good surface finish properties on machined parts with minimal dimension extension. This article reviews the black oxide coating process, different types of black oxide finishes, their applications, and everything you need to know about this distinctive surface finish.
What Is Black Oxide Coating?

Black oxide is a chemical conversion process to blacken a part’s surface without adding a thick coating. Unlike plating or coating, which adds a thicker layer on top of the base material, a chemical conversion process uses a chemical solution to force a reaction on the part’s surface.
Although black oxide is most commonly applied to ferrous metals (metals containing iron), there are methods for black oxideing other metals, such as copper and stainless steel, specifically designed to resist surface reactions. The finish is typically black or a dark bluish-black. It can be glossy or matte, depending on the pre-process finish and the post-conversion treatment used after blackening.
There are several different names for black oxide. Some of the names for similar black oxide processes are black oxide, blackening, bluing, cold bluing, and gun bluing. There are some minor differences that we will go over later. Some sources incorrectly combine black phosphate and black oxide processes. Both processes can result in a blackened surface but are not the same.
What Is the Process of Applying Black Oxide Finish?

There are five major steps involved in the black finish process, and they are:
Cleansing
The metal surface is cleaned properly to remove contaminants like grease, oils, rust, or dirt. This step is essential to ensure proper adhesion of the black oxide coating.
Rinsing
After cleansing, the metal is rinsed to remove any remaining cleaning agents or debris. Rinsing helps prepare the surface for the next steps in the process.
Descaling/Pickling
In this step, the metal is treated with a descaling or pickling solution to remove any scale, oxides, or other impurities from the surface. The purpose is to create a clean and reactive surface for the subsequent blackening process.
Neutralizing
This process is only required when the finished parts have blind holes or are part of an assembly. This entails rewashing the part with an alkaline solution. This will help prevent bleed-outs, which could damage the part’s surface.
De-plating
This conditional stage is only present when the finished part is plated with another material (chromium, zinc, cadmium, etc.). The machinist must de-plate the part because the black oxide gun finish cannot be maintained on plated parts.
Black Oxide Finish
The machinist will finally apply the finish here. The finished metal parts are dipped into tanks containing various alkaline solutions, such as sodium hydroxide and nitrates. This stage has three temperatures that determine the coating material on the part’s surface.
The process leaves a magnetite coat (Fe2O3) on the part at both high (141°C) and low (90-120°C) temperatures. The method, however, deposits a copper selenium coat (Cu2Se) on the part surface at the cold temperature operating level.
After-Finish
The finished part is still prone to corrosion without the after-finish. This rule, however, does not apply to surfaces made of black oxide stainless steel or brass. This is because these metals are naturally anti-corrosive. For other metal parts, however, the after-finish is critical. Oil, wax, and lacquer are popular after-finish options.
Oil is the most common after-finish used by machinists. It creates a glossy surface while also improving lubrication and corrosion resistance. Wax produces a duller surface but has superior lubrication and corrosion-prevention properties. Lacquer is also a good option, especially if you need to finish the parts quickly.
Types of Black Oxide Finish
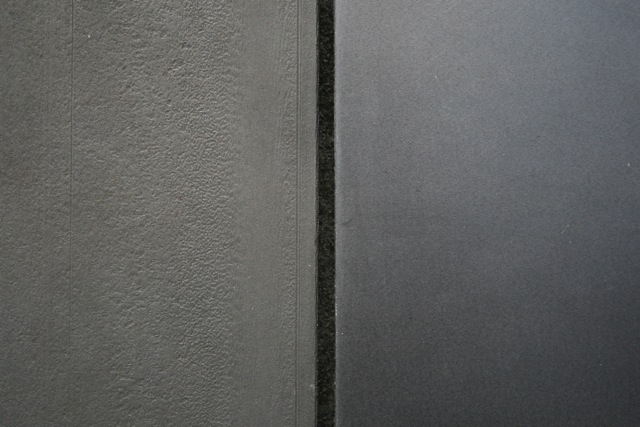
As mentioned earlier, there are various operating temperatures at which machinists carry out the black oxide finishing process. These temperatures also differ in the different types of black oxide finish. They include:
Hot Black Oxide Finish
The hot black finish is the type of black oxide finish that is most commonly used. It entails submerging the component in hot salt baths. Caustic soda (NaOH), nitrates, and nitrites salt baths are among the kinds of salt baths employed. Automated transporters move the parts from one bath to another, impacting the process completely. This process typically operates in the 275°F to 295°F temperature range.
Maintaining this temperature range is crucial for the black oxide coating process. This is because the process takes longer at lower temperatures, whereas the surface of the completed part would rust at higher temperatures. Instead of rust, another iron compound, magnetite (Fe2O3), is formed due to the salts and the elevated temperature of the slats.
Another method of applying hot black oxide coating is used rarely. It involves the use of iron (III) chloride. However, it only works on steel surfaces. The machinist repeatedly immersed the steel part in an iron (III) chloride bath and then in a hot water bath.
Mid-temperature Black Oxide
The operating temperature is the only difference between this process and the hot black oxide finish. This location has an operating temperature between 194°F and 248°F. The metal may also turn into magnetite at this temperature. However, it has an advantage over the hot black oxide finish, which doesn’t release caustic fumes while working.
Cold Black Oxide
This method differs from the other types and is called room-temperature black oxide. This procedure applies copper selenide to the metal surface between 68 and 86°F. This method produces a black oxide finish, which isn’t as wear-resistant as the other finishes. But, it becomes equally good after the after-finish is added.
Materials for Black Oxide Finish

The following materials are compatible with a black oxide coating:
Carbon Steel
Because of its durability and corrosion resistance, black oxide coating is commonly used on carbon steel parts. It is frequently used on machine parts, tools, and fasteners.
Stainless Steel
Stainless steel is frequently used in harsh environments because of its high corrosion resistance property. Stainless steel parts can benefit from an additional layer of protection from black oxide coating.
Copper
To achieve an ebonol c finish, black oxide coating is frequently applied to copper parts. This is a popular finish for plumbing fixtures, electrical components, and decorative items.
Zinc
Black oxide coating can also create an ebonol z finish on zinc parts. This finish is frequently applied to hardware, automotive parts, and decorative items.
Brass
Brass is a material that is frequently used in decorative applications. On brass parts, black oxide coating can create a distinctive and long-lasting finish.
Aluminum
Aluminium parts can be given a black finish by applying a black oxide coating. This finish is frequently used for decorative purposes and can provide additional corrosion protection.
Pros and Cons of Black Oxide Finish
There are several advantages of using the black oxide finish for your parts. However, it has its disadvantages. This section explains some of the pros and cons of black oxide finish:
Pros
- Improved Protection Against Corrosion: The black oxide finish’s superior resistance to metal corrosion is one of its main advantages. It creates a protective layer that gives your metal components the sturdiness required to withstand deterioration over time.
- Diminished Light Reflection: Black oxide is your best option if you’re looking for a non-reflective surface. For optical devices or other applications where glare can be bothersome, it’s perfect.
- Visual Appeal: Black oxide’s smooth, dark finish gives your metal components a polished, industry-standard appearance.
- Primer for Additional Finishes: If you wish to apply additional metal surface treatment to your part, black oxide works great as a primer.
Cons
- Corrosion Resistance: Although a black oxide finish is porous and readily absorbs oil, corrosion protection is limited to the oil or other sealant used on the surface. Black oxide is among the worst metal finishes available in terms of corrosion resistance.
- Durability: A good black oxide finish shouldn’t rub off or flake, but it isn’t as durable as many other finish choices.
Applications of Black Oxide Finish for Precision Machined Projects
Here are some of the most common applications for black oxide finish for precision machined projects:
- Medical applications: Black oxide surface parts can absorb light, making them suitable for use in photosensitive medical devices like X-ray machines.
- Assembly tool: Component manufacturing precision machine tools are typically finished in black oxide. Good examples of such tools are bearings, fasteners, and gauges.
- Auto parts: Black oxide finish is also used on many auto parts. They are in parts like spark plugs, oil filters, suspension bushings, brake valve components, etc.
- Electrical components: Electrical components with a black oxide finish include strippers, timer gears, cutters, etc.
What Are the Factors to Consider When Using Black Oxide Finish

There are some things to note before considering the black oxide finish process, and they are:
Part Applications
Do you produce precision machined parts for the aerospace industries? Or are your parts meant for the medical or automotive industries? These are questions for which you ought to know the answers already. As such, the responses to these questions will determine your manufacturing decisions. In the end, the black oxide finish is adaptable and works well for various applications across various industries.
Location
When choosing black oxide as a finish, it’s also important to consider where you plan to use the part. When applied indoors, surface finishes typically have longer lifespans. Black oxide follows the same guidelines. Owing to its thin layer, black oxide may fade more quickly in outdoor environments with high humidity and constant temperatures.
Desired Appearance
Components used in certain applications must come with some quality aesthetic finish. Some parts may require a matte or glossy finish. This will affect how thick the application of the black oxide will be. So, the desired finish appearance is another crucial consideration.
Intended Duration of Use
Choosing the appropriate surface finishing for precision machined parts depends on how long you plan to use them. Because black oxide doesn’t rust, it can last very long. However, other factors like the part’s application and usage location affect this factor.
Common Defects and Solutions for Black Oxide Coating
Here are some common defects encountered when you use black oxide coating, as well as the solutions to these defects:
Grey Finishes
When the black oxide metal finish appears with a grey tint instead of the expected black colour, it’s usually due to temperature fluctuations during the black oxide coating process. To address this issue, ensure that the temperature of the salt baths remains at a predetermined level and is consistently maintained throughout the process.
Brown Rub-offs
When rubbed on the surface, Brown rub-offs happen when a precision-machined part shows a brown (rusty) colour. This problem is often caused by a high concentration of colloidal iron in the salt bath or the use of higher temperatures than required.
If you notice brown rub-offs, replace the salt baths being used and verify that the salt bath temperature is at the specified level. This should completely resolve the problem.
Black Oxide Finish Discontinuities
Discontinuities in the black oxide finish occur when certain patches of the finished part are not adequately covered. This is usually a result of impurities on the surface of the metal part.
To address this issue, rerun the part through the cleansing process. After ensuring proper cleaning, you can repeat the black oxide coating process for a comprehensive and uniform finish.
Performance Tests for Black Oxide Finish
The two popular performance tests for black oxide finish are:
Smut Test
This procedure involves testing the finish’s durability on the metal surface physically. Verifying if there is any black residue on the metal surface is also beneficial. Before applying the after-finish, the machinists appear to rub their hands over the metal’s surface. If there is a problem with the black oxide coating process, the finish will rub off. The procedure is deemed successful if not.
Relative Humidity Test
This test shows how resistant the black oxide part is to corrosion. The test examines the black oxide part’s ability to withstand water at 100% relative humidity.
Choosing Black Oxide Finish for Your Precision Machined Parts
Surface finishes on precision machined parts are an important way to improve the quality of these parts. Black oxide finish is popular because of its low application cost and wide range of applications. While the finish on machined parts is excellent, getting it done correctly requires expertise in the machining field.
Zintilon has the expertise required for various surface finishing processes such as anodizing, plating, polishing, painting, sanding, etc. Apart from surface finishing, we can handle your precision machining processes from start to finish. We have experts in various rapid prototyping services, ranging from CNC machining to many more. Get a quote today to get started!